- Printing and finishing with conventional and UV inks/coatings
- High automation for fast makeready
- Production speeds up to 18,000 sheets per hour
- Cutting-edge quality control and reporting
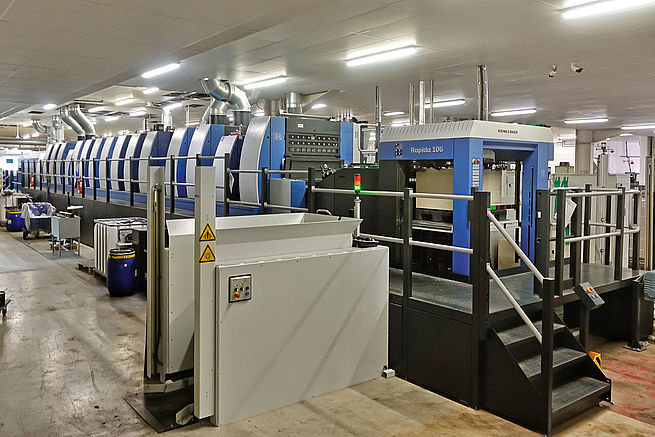
A few days ago, a new Rapida 106 went into production at Saica Pack Dublin. The press in question is an individually tailored medium-format installation (for sheet formats up to 740 x 1,060 mm) with a total of 15 printing and finishing units and an overall length of 32 metres. The configuration is as follows: a printing unit, coater and two intermediate drying towers, followed by an adaptable perfecting unit, seven further printing units, another coater, two more intermediate drying towers, a third coater and a three-section extended delivery. The Rapida 106 stands on a 900.mm base and is equipped with pile logistics for the feeder and delivery.
The new press has been purchased to print and coat high-quality packaging with up to seven colours and additional finishing, including products with printing and finishing on both sides of the sheet. Saica Pack produces corrugate supplies for major brands from across Great Britain and Ireland – including well known names in the food and fashion industries.
Saica Group operates plants in a total of nine European countries, as well as in the USA. They serve four business areas: waste management, paper recycling and corrugated board production, board packaging and flexible packaging. The Group currently has five plants across the Republic and Northern Ireland alone.
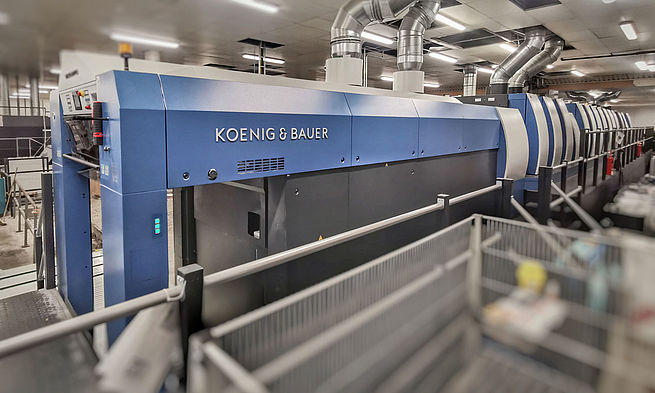
Outstanding automation
The Rapida 106 incorporates accessory packages for board printing and plastic films and in this way grants Saica Pack’s exceptional flexibility with regard to substrates. This comes in addition to the equipment for UV/mixed operation, which permits the use of both conventional and UV inks and coatings. The UV process, in particular, enables high-quality finishing in a single press pass.
The outstanding automation solutions of the Rapida 106, which is engineered for production speeds up to 18,000 sheets per hour in straight printing mode, include DriveTronic SPC for simultaneous plate changing, CleanTronic Multi washing systems in conjunction with DriveTronic SRW (simultaneous roller washing), and Anilox Loader for automatic anilox roller exchange. QualiTronic ColorControl and QualiTronic PrintCheck control the colour in an inline process and compare the printed sheets with a defined reference. Process-free printing plates are used, and these plates can also be mounted on the printing units without prior bending.
Colour control and sheet inspection were two of the critical factors which clinched the deal for the Rapida 106: Every single sheet is measured, a control check takes place every tenth sheet. The control and reporting functions consider each individual ink zone and not just an average over the whole sheet. Furthermore, the sheets are fully printed and finished at the time of measurement, which means that the QualityPass reports provide an accurate assessment of the overall process – an important factor for ISO certification of the packaging production. The facility to disengage printing units which are not required for a particular job was a further feature which favoured the Rapida 106. The effect is greatly reduced roller wear. The short-train inking units also switch the press to colour mode in next to no time, which reduces waste and makeready costs.
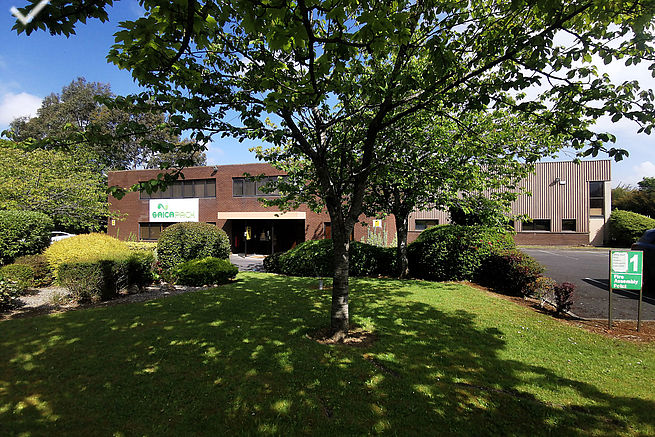
Rapida presses in use across Europe
Sheetfed offset presses from Koenig & Bauer are also in use in other plants operated by Saica Group, for example in Spain, France and Italy. In almost all cases they are large-format models from the Rapida 142 press series (max. sheet format 1,020 x 1,420 mm) and Rapida 162 (sheet format up to 1,200 x 1,620 mm) – with up to 11 printing and finishing units per press.